Seema Kamath
Grip 'n Torque, Gadgetry: Sensors, Actuators, and Processors,
Team of 3, Fall 2019


We powered the vertical motion with a stepper motor driving a lead screw and balanced the bending moment from the top plate with linear bearings on the other two columns. The vertical motion was stopped when a limit switch was pressed. The horizontal motion powered by two gear-motors with built in encoders utilized the self-centering clamp design. Motion on the bottom was stopped by a pressure sensor. Rubber erasers provided enough friction to clamp the containers and had rigid backing so that they could be pre-curved and better conform to the container shape. For unscrewing caps, we had a smaller DC motor and had high friction neoprene wheels in place of grippers.
The project for this class was to create a gadget that would be an assistive device enabling every day life. Our group decided to go all out and make a device that would automatically open both bottles and jars at the push of a button. I utilized SolidWorks to create much of the mechanical system shown as well as wired up many of the sensors and motors. Overall, our project was a success. As shown from the below videos, we were able to make the top platform descend to the bottle or jar at the push of a button, clamp it on the bottom and top, unscrew a cap, and everything move back into the original position. While in the time we had, the device was not able to do everything at once, each subsystem worked. The only thing stopping us from it being seamless was the DC motor than spins off the cap which malfunctioned for a bit. We did fix it by hitting it lightly with a hammer, but with the time left did not get current sensing to sense when the cap was gripped in time.


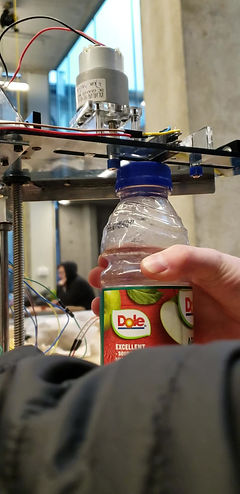
Fully clamping to a bottle
Showing full movement of gadget
(with extra button click for gripping of cap)
Spinning off a cap
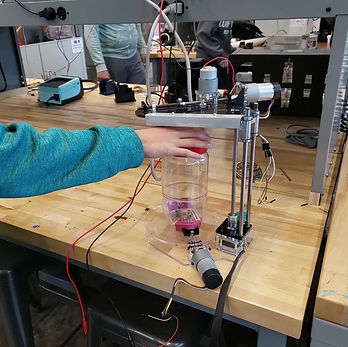
